Slag Steel Silo
Just as its name implies, is generally used for storing slag, it also can be called slag storage tank. Our slag steel silo contains a main body which stores slag, and a plurality of filters that are arranged on a wall surface of the main body and cause a liquid to selectively pass therethrough. The slag steel silo is made of high quality double-side galvanized steel sheets with spiral folding machines. The main technology is spiral. Spiral steel silo is one of the superior steel structure for slag storage. We have professional construction team, can help our customers to built slag steel silo on-site. There are two structures of spiral steel silo’s on ground foundation, namely, steel structure which is usually for the small size steel silo with the capacity lower than 1500 ton. Concrete structure foundation which is suitable for either small or large capacity silos. Besides slag, other mineral powders also can be stored by the spiral steel silo.
Advantages of Slag Steel Silo
Low investment: The total cost of spiral steel silo is 30 to 50 percent lower than that of reinforced concrete silo, at the same time, we guarantee the quality of our steel silo.
Various models for different sizes: our company can produce steel silos with capacity from 50 ton to 15,000 ton. The silos’ diameter changes from 3 meters to 30 meters, and all our steel silos are in cylinder shapes. There are complete accessories and functions that can meet the requirements of different clients. And various capacities and sizes ensure our slag storage silos suitable for different scale of plants.
Anti-corrosion and moisture proof: our steel silos are moisture proof and anti-corrosion because they adopt high quality galvanized steel. The edge of spiral silo is five times thicker than that of silo shell, which ensures no leakage of powder, even air.
Professional working team: our construction team will offer technical guidance from the beginning design to the end construction, during the application process of slag storage, our experts are ready to answer any questions at any time in order to provide your the best service.
Excellent after sales service: after the steel silo is finished, we provide one year maintenance for free. And after receiving feedback we ensure a timely reaction for arriving at the scene in 36 hours. Besides, once you have any question, we can supply free guidance.
Slag Steel Silo Construction
- The flat ground is selected as the construction platform for the slag steel silo, including the main structure, the steel frame, the steel column and the connecting machine .
- Set the molding machine, bending machine and support frame horizontally.
- Place the coil into the molding machine.
- Use a bending machine to feed the bent bite into the spiral rib 5 times the thickness of the silo body.
- When the height of the silo reaches 2m, the top of the silo body is cut horizontally by an automatic cutting machine.
- Install the silo ceiling.
- Using a bending machine, the silo body is constructed according to the designed silo height.
- According to the reinforcement drawing, weld the reinforcement to the inner wall of the silo.
- Use a cutter to cut the bottom of the silo body horizontally. (This step is built at the same time as step 8).
- Reverse the silo to the silo floor and drop to the pre-buried steel.
- Connect the ribs to the embedded parts to complete the rooting work.
About Slag
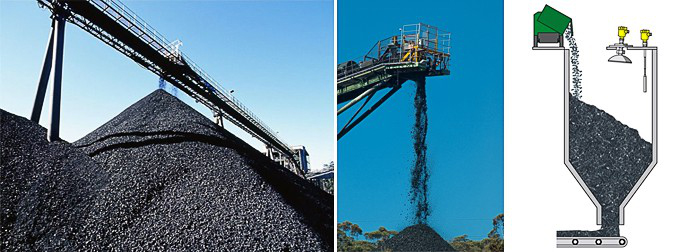
Slag is a glassy by-product produced by separating the desired metal from the ore. Typically, slag is a mixture of metal oxides and silica, but may also contain metal sulfides and elemental metals. Slag is generally used to eliminate waste in metal smelting, and may also have other effects, such as assisting the temperature control of the smelting, minimizing the degree of re-oxidation of any final liquid metal product before the molten metal is removed from the furnace, and producing a solid metal, etc.
Slag storage silo
The bottom of the slag steel silo can be divided into two types: conical hopper bottom and flat bottom. The conical hopper bottom silo can only be a small capacity silo with the capacity of no more than 2,000 tons. However, in order to ensure the smooth discharge of slag powder, some auxiliary equipment will be installed in the silo, such as the vibrator on the silo hopper and the aeration tank on the silo hopper. The flat bottom silo always has an inverted cone at the bottom of the silo, which serves to reduce the pressure at the center of the silo. For this type of silo, the inverted cone prevents the slag powder from flowing directly to the aeration tank. The aeration tank is designed to allow the slag powder to drain smoothly (please note that there are multiple inverted cones at the bottom of some large slag tanks).